HACCPに沿った衛生管理では、「衛生管理計画の作成」とその計画を実施した「記録の保管」を行うため様々な文書の作成が必要となります。文書の作成を進めるなかで、多くの企業が以下のような問題を抱えています。
・それぞれの文書の書き方やルール、管理項目が決まらない
・フローダイアグラムやハザード分析表など、複数文書の整合性をとるのが難しい
・文書の作成、管理に多大な時間と労力がかかる
これらの問題をクリアし、文書作成をいかに効率的に行うかが、HACCPに沿った衛生管理を成功させるためのポイントです。
HACCP(ハサップ)とは?
HACCPとは、安全を阻害する要因を特定し、原材料の受入から製造・出荷へと続く食品製造工程のなかで、危害の防止につながるポイントを継続的に管理して、食品の安全を確保する衛星管理法です。
食品衛生法の改正により、HACCPは2021年6月から完全義務化となりました。
HACCP(ハサップ)と従来の検査・管理方法の違い
従来の検査・管理方法では、最終製品の抜き取り検査をしていたので、基準に満たない商品がチェックをすりぬけて市場に出てしまうリスクがありました。
(抜き取り検査とは、出荷段階にある製品をランダムに抜き取り、その製品の 品質 をチェックする検査方法のことです)
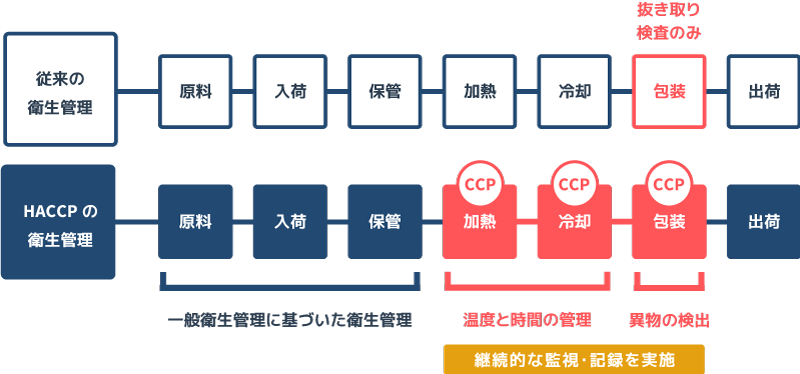
HACCP(ハサップ)導入のメリット
HACCPは製造工程ごとに管理できるので、危険因子の混入・汚染などを防ぐ対策ができ、結果的にクレーム・事故の減少に繋がります。 国際基準で展開されるHACCPを導入することは、大きな宣伝材料にもなります。
企業価値が高まり、取引先の信頼や評価に繋がるだけではなく、人材確保の面でも役立つでしょう。
実際に、令和3年での公益社団法人日本食品衛生協会の調査によると、HACCPに沿った衛生管理を導入したことにより、「品質・安全性向上」、「製品イメージ、企業(店舗)イメージの向上」、「従業員の意識の向上」などの効果が得られていることがわかります。
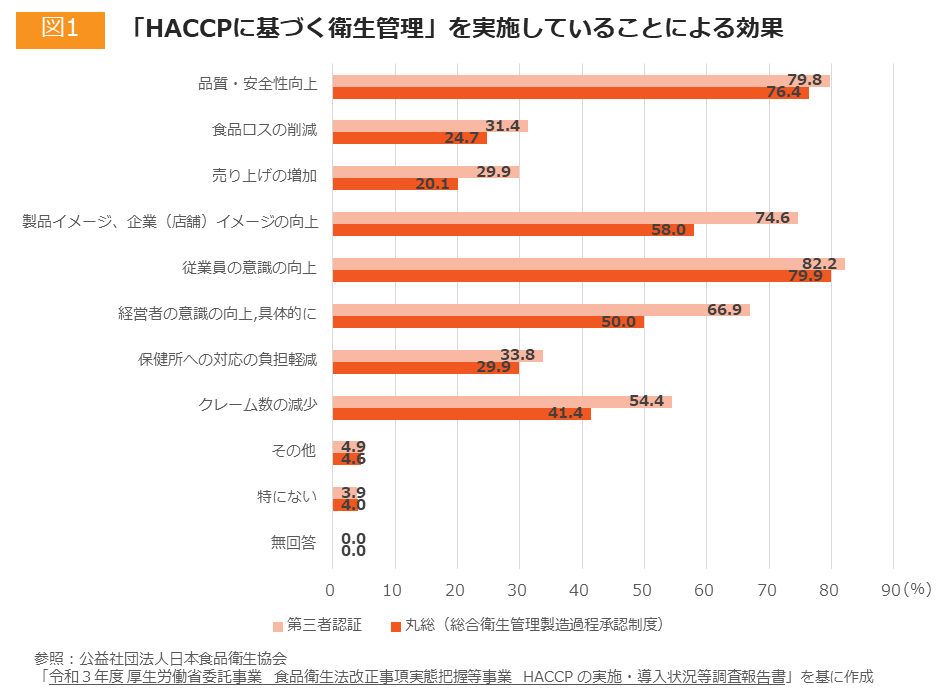
HACCP(ハサップ)を構築するための 7原則12手順
では、HACCPを構築するための手順について説明していきます。
HACCPの構築の手順は「7原則12手順」として示されています。
7原則12手順では各工程の段階でリスクを大きく軽減することができ、より効果的に安全性に問題のある製品の出荷を防止できるとされています。
「7原則12手順」は「7原則(手順)」と、7原則の前準備のための「5手順」から構成されています。
手順1~5は、HACCPプランを作成するための準備です。流れがわかりやすいよう、「5手順」から紹介します。
手順1 | HACCPチームの編成 | 製品を作るために必要な情報を集められるよう、各部門から担当者を集めます。 (※HACCPに関する専門的な知識を持った人がいない場合は、外部の専門家を招いたり、専門書を参考にしても良い) |
---|---|---|
手順2 | 製品説明書の作成 | 製品の安全について特徴を示すものです。特性や原材料等をまとめておくことで、危害要因分析の基礎資料となります。 |
手順3 | 意図する用途及び対象となる消費者の確認 | 用途は製品の使用方法(加熱の有無等)を、対象は製品を提供する消費者を確認します。 |
手順4 | 製造工程一覧図の作成 | 受入から箱詰めまでの流れを工程ごとに書き出します。 温度や時間、速度、濃度などの設定に加え、汚染区域と清潔区域の区分線を引くと、工程の重要度が明確になります。 |
手順5 | 製造工程一覧図の現場確認 | 製造工程図ができたら、原料の入荷~製品の出荷までの現場での人の動き、モノの動きを確認して必要に応じて工程図を修正しましょう。 |
手順6 【原則1】 | 危害要因分析の実施 (ハザード) | 工程ごとにどのような危害要因があるか考えます。 原材料に由来するものや工程中に発生しうるもの等を列挙し、管理手段を挙げていきます。 |
手順7 【原則2】 | 重要管理点(CCP)の決定 | 危害要因を除去・低減すべき特に重要な工程(管理点)を決定します。 |
手順8 【原則3】 | 管理基準(CL)の設定 | 危害要因分析で特定したCCPを適切に管理するための基準(例えば温度、時間、速度など)を設定します。 |
手順9 【原則4】 | モニタリング方法の設定 | CCPが正しく管理されているかを適切な頻度で確認し、記録します。 (CLに達しているか常時確認することをモニタリングといいます) |
手順10 【原則5】 | 改善措置の設定 | モニタリングの結果、CLが達成されなかった時に 製造工程の中で発生した問題点を修正し、是正することをいいます。 |
手順11 【原則6】 | 検証方法の設定 | これまでで作成されたHACCPプランに従って管理が行われているか、修正が必要かどうか検討します。 |
手順12 【原則7】 | 記録と保存方法の設定 | 記録はHACCPを実施した証拠であると同時に、問題が生じた際には工程ごとに管理状況を遡り、原因追及の助けとなります。 記録・保存方法をあらかじめ決めておくとよいでしょう。 |
HACCP(ハサップ)の導入時の課題
HACCPを構築していくには、「危害要因の分析の実施」や「管理基準の設定」、「記録と保管方法の設定」など、上記に記載した12の手順に沿って進めなくてはいけません。
手順が細かくて難しく感じるかもしれませんが、どれも重要です。
HACCP導入における課題としては、主に以下のものが挙げられます。
- それぞれの文書の書き方やルール、管理項目が決まらない
- フローダイアグラムやハザード分析表等、複数文書の整合性をとるのが難しい
- 文書の作成、記入する帳票が大量であることにより、管理に多大な時間と労力がかかる
効率的に整合性のとれた文書作成・修正を実現するには
上記の課題を解決し、HACCPに基づく管理・記録を円滑化するためには、以下のポイントを押さえることが大切です。
- ペーパーレス化を促進し、情報を一元管理する
- ツールの活用により各プロセスを自動化する
効率的に整合性のとれた文書作成・修正を実現するためにシステム・ツールの活用をお勧めいたします。
HACCP文書を効率的に作成・メンテナンスできる専門ツール
HACCP文書作成ツール「HACCPクリエータ」
「HACCPクリエータ」は、フローダイアグラムの作成・修正機能やハザード分析表・HACCPプランの自動出力・取込機能により、HACCP文書の作成・維持管理工数を大幅に削減することができるHACCP文書作成の専門ツールです。
HACCP文書作成ツール「HACCPクリエータ」の主な特徴
圧倒的な生産性を実現するフローダイアグラム作図機能
HACCPに沿った衛生管理を行う際、「プロセスの記述」に使用されるフローダイアグラムですが、作成には時間と手間を要します。
「HACCPクリエータ」では、図形パレットから図形を選択し、配置するだけです。図形をドラッグして引っ張るような感覚で、初心者でも素早く簡単にフローダイアグラムを作成することができます。
接続線の繋ぎ直しや線跨ぎの自動変換などの様々な自動補正機能により、直感的で快適な作図作業を実現します。
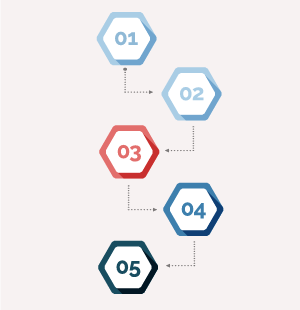
完全に整合性の取れた管理表類の自動出力・取込機能
数回のクリック操作だけで、自動的にエクセル形式のハザード分析表やOPRP/CCP表をフローダイアグラムと整合性を保った形で出力できます。
出力された管理表類をエクセル上で修正して取り込むと、フローダイアグラムに修正内容を反映させることも可能です。
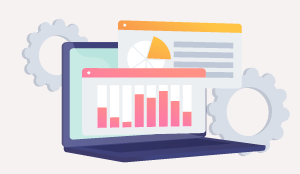
製品・サービスに関する詳細、
カタログダウンロードはこちらから
HACCP文書作成ツール「HACCPクリエータ」
HACCP文書作成ツール「HACCPクリエータ」はフローダイアグラムの作成・修正における圧倒的な生産性と、ハザード分析表・HACCPプランの自動出力・取込機能により、HACCP文書の作成・維持管理工数を大幅に削減するHACCP文書化専門ツールです。
作成したフローダイアグラムに工程情報、危害情報を登録し、ハザード分析表、HACCPプランを簡単に出力・作成できます。
カタログダウンロード

【参考】 ・公益社団法人日本食品衛生協会「令和3年度 厚生労働省委託事業 食品衛生法改正事項実態把握等事業 HACCP の実施・導入状況等調査報告書」