2025年、食品製造業の“現場安全”は大きな転換点を迎えています。例年7月に「全国安全週間」が実施されていますが、2025年はさらに重要な制度改正が加わりました。それが、2025年6月施行の「熱中症対策義務化」です。これまで「安全」は、個人の意識や経験に依存しがちでした。しかし、法制度が“安全は企業の義務”と定義した今、現場安全の在り方そのものを抜本的に見直す必要があります。
本稿では、制度対応にとどまらない、文化としての安全の定着、ITを活用した仕組み化、そして企業の現場がどう変革できるのかを、多面的に解説します。
1. 熱中症対策義務化が突きつける、感覚から仕組みへの転換
食品製造の現場は、冷却・加熱・蒸気・洗浄といった工程が混在し、マスクや衛生服の着用も義務づけられるため、熱ストレスが高まりやすい環境です。しかも、空調が届きにくいエリアや夜間作業など、負荷のかかる条件が重なる現場も少なくありません。
2025年6月1日より、労働安全衛生規則の改正省令が施行され、特定の条件下での作業を行う事業者に対し、熱中症対策が法的に義務付けられました。
1-1. 熱中症対策義務化の概要(2025年6月1日施行)
対象となる作業条件
- 作業環境:WBGT(暑さ指数)28度以上、または気温31度以上
- 作業時間:連続1時間以上、または1日4時間以上の作業
1-2. 企業に求められる3つの対策
- 報告体制の整備(見つける)
熱中症の自覚症状がある労働者や、他者の異常に気付いた者が速やかに報告できる体制を構築し、関係者に周知する。 - 実施手順の作成(判断する)
熱中症の疑いがある場合の対応手順(作業からの離脱、身体の冷却、必要に応じた医療機関への搬送など)を定め、関係者に周知する。 - 関係者への周知(対処する)
上記の報告体制や実施手順を、ポスター掲示、朝礼での説明、文書配布などを通じて、関係者全員に周知徹底する。
1-3. 対策を怠った場合の罰則
これらの義務を履行しなかった場合、事業者には以下の罰則が科される可能性があります。
- 6カ月以下の拘禁刑
- 50万円以下の罰金
また、労働基準監督署からの是正勧告や報告命令を受けることもあります。この改正は、熱中症対策を「やっているつもり」から「確実に実行される仕組み」へと移行させるものです。特定の個人任せではなく、職場全体が一体となって「見つける・判断する・対処する」体制を構築することが問われています。
食品製造のように熱ストレスが避けにくい現場こそ、属人的な経験や感覚に頼らない明確な基準と即応体制が不可欠です。熱中症は防げる災害であり、企業の安全配慮義務が厳格化された今こそ、現場の“当たり前”を仕組みで守る転換点を迎えています。
2. 全国安全週間は“イベント”ではなく“文化の入口”に
厚生労働省では、令和7年度(2025年度)も全国安全週間を実施します。期間は7月1日(火)から7日(月)まで、その準備期間は6月1日(日)から30日(月)までです。令和7年度のスローガンは、全国からの応募の中から選ばれた、東京都・小澤正紀さんによる以下の作品です。
〈令和7年度 全国安全週間スローガン〉
多様な仲間と 築く安全 未来の職場
全国安全週間は、今年で98回目の開催となります。労働災害を防止するために、産業界における自主的な活動を推進し、安全意識の向上と活動の定着を図ることが目的です。これまで、労使が協調して取り組んできたことで、労働災害は長期的には減少傾向にあります。しかし、令和6年の死傷災害(休業4日以上)は前年を上回り、転倒・腰痛・墜落・転落などの災害が依然として多く発生しているのが現状です。
このような状況の中、労働者一人ひとりが安全に働ける環境を整備するには、令和5年3月に策定された「第14次労働災害防止計画」に基づき、着実に施策を推進していく必要があります。令和7年度はその計画年次3年目にあたり、引き続き労使が一丸となって取り組むことが求められています。厚生労働省は、全国安全週間において、職場での巡視・スローガン掲示・労働安全講習の開催などを推奨しています。
2-1. 食品製造業に求められる「安全文化」への本質的転換
とりわけ、食品製造業界は、他産業に比べて特有の安全リスクを抱えています。高温・低温環境が混在し、加熱・冷却・蒸気処理・薬液洗浄といった多様な工程が同居しており、かつマスクや防護服の着用、時間厳守の作業ルールが日常的に課されるため、作業者の身体的・精神的な負荷が高まりやすいのです。そのため、「安全=道具や設備だけの問題」ではなく、「職場風土そのものの問題」として捉える必要があります。実際、現場における不安全行動や事故の芽は、「形式的なルール」ではなく「見えない慣れや空気」の中で育ってしまうのが現実です。
2-2. 安全週間を“変える入口”と捉える企業の実践
しかしながら、多くの現場では、全国安全週間が単なるポスター掲示や訓示で終わる“イベント化”しているケースも見受けられます。これでは、事故の芽を摘むどころか、「気づけない職場」を温存するリスクさえあるのです。ある食品企業では、全国安全週間を“見せるイベント”ではなく“変えるプロセス”と再定義しています。以下のような具体策に取り組んでいます。
- 前年に発生したヒヤリ・ハット事例を部署ごとにレビューし、根本原因を対話的に分析
- 市販ポスターではなく、現場の気づきから生まれた“手描き安全ポスター”を製作・掲示
- 7月だけで終わらせず、「7月+8月+9月」の3か月を“安全重点期間”とする独自運用
- 各部門が自ら主導する「安全点検ラリー」や「危険予知ワークショップ」により、当事者意識を醸成
こうした取組は、単に安全週間を“頑張る一週間”にとどめるのではなく、「11か月の安全を育てるための“文化醸成月”」として位置づけ直すことに成功しています。
2-3. 「形式」ではなく「気づきの文化」へ──5つの具体的提言
令和7年度のスローガン「多様な仲間と 築く安全 未来の職場」は、まさに現在の食品製造業に最も必要とされる方向性です。日本語に不慣れな外国人技能実習生、派遣社員、夜勤・交代勤務者、女性や高齢者など、“多様な属性と事情を持つ労働者”が混在する食品業の現場では、安全の前提となる「共通理解」や「共通言語」の不在こそが、大きなリスク要因になります。だからこそ、「形式的な安全」ではなく、「自分ごととして気づき合える安全文化」を育てる必要があります。その実現に向け、以下の5つの提言を具体的に挙げます。
提言①:「見える化」ではなく「話せる化」へ──1日1分の“安全対話”を制度化
朝礼や昼礼での「ヒヤリ・ハット共有」や「昨日の作業で感じた違和感」を、1日1テーマ・1人1分で交代制にするなど、全員参加型の安全対話を仕組みに落とし込むことが重要です。ポスターやKY(危険予知)シートだけでは届かない“本音のリスク”が浮かび上がる場になります。
提言②:「気づきメモ」運用の推奨──日々の小さな違和感をログ化する
形式的な点検表では見落とされがちな“現場のささいな変化”をキャッチするため、作業中に気づいたことをすぐ書ける「気づきメモ」ツール(紙・タブレット・アプリ)の導入を提案します。一定期間でメモを集計し、改善提案につなげることで、現場発の改善ループが動き始めます。
提言③:“一部の人が頑張る”から“全員の自発性を引き出す”へ
リーダーや安全担当者が旗を振るだけでなく、「部門ごとに自由に取り組む安全強化策」を考えて発表・実行する時間を、安全週間中に最低1回確保します。
テーマは自由に(例:「私たちの職場で一番事故が起きそうな場所はどこか?」など)、現場の言葉で安全を語る機会を設けることが鍵です。
提言④:外国人・派遣社員にも届く“伝え方の翻訳”を整備する
特に外国籍労働者にとっては「安全」は“言語バリアのある世界”です。多言語ピクトグラムの掲示や、母語の“やさしい日本語”解説資料を安全週間中に配布することで、形式で終わらない「本当に伝わる教育」に近づきます。
提言⑤:「7月の取り組み」を「8月以降に接続する仕組み」を作る
安全週間で出てきた気づきや課題を“やりっぱなし”にしないために、「1か月後の振り返り日」を最初から設定し、取組内容のレビューと改善報告を実施します。
7月の行動が、8月以降の現場改善につながる“仕組みのスタートライン”として機能させることが大切です。
これらの実践は、多様な仲間と安全を築くための“実装型アプローチ”です。安全文化とは、スローガンや訓示ではなく、日々の現場の“仕草と態度”の積み重ねで根づきます。だからこそ、全国安全週間を「ただやる」1週間から、「変わるきっかけ」としての1か月に進化させることが、今まさに求められています。
3. ヒヤリ・ハットは“改善の種”である 〜食品業の現場にこそ根づかせたい「気づきの連鎖」〜
「ヒヤリ・ハットが出ない職場=安全」と考えていませんか?実は、その逆です。ヒヤリ・ハットが報告されない職場は、“気づけていない”か、“黙殺されている”かのどちらかであり、重大災害の予兆が見過ごされている危険な状態といえます。ハインリッヒの法則(1:29:300)では、1件の重大事故の背後には、29件の軽微な事故と、300件の事故未遂:ヒヤリ・ハットがあるとされます。つまり、ヒヤリの報告件数が多い職場ほど、安全文化が成熟しているのです。
3-1. 食品製造業に特有の“ヒヤリ”とは?
食品業の現場では、ヒヤリ・ハットの内容も特有のものが多く存在します。
たとえば:
- マスクや衛生服による視界不良・聴覚遮断
- 蒸気や熱水使用による滑り・やけどのリスク
- コンタミ(異物混入)への過剰な緊張から生じる焦り・動線ミス
- 機械設備の洗浄・分解時のシャープエッジや熱残り
- 深夜・早朝勤務による注意力低下と反応遅延
これらは、工業系製造とは異なる「衛生管理と作業安全の両立」が求められる食品製造ならではのヒヤリであり、一人の不注意が「品質事故」や「異物混入」に直結する重大性を持っています。
3-2. 成果を出している職場に共通するヒヤリ活用の工夫
実際に安全文化を根づかせている企業では、以下のような仕組みづくりが行われています。
- ヒヤリ報告=改善提案として表彰対象に(インセンティブ設計)
→ 毎月MVP表ヒヤリ報告=改善提案として表彰対象に(インセンティブ設計)、部門単位での提出率ランキング - 5分以内で入力できるスマホ報告フォーム
→ 実作業者が衛生手袋のままでも入力可能なUI設計に - 毎週の朝礼で1件ピックアップし、全員で再発防止策を討議
→ 品質ミスとの因果関係まで掘り下げ、次工程への影響も確認 - 「同じヒヤリ」が発生したら、部門全体で再設計まで行う
→ 工程変更・設備改善・掲示物の見直し等まで完結させる体制 - 外国人従業員やパート社員の報告がしやすいよう、イラスト・母国語での記載例やタブレット入力補助を整備
3-3. 「報告すると怒られる」から「報告すると職場が良くなる」へ
ヒヤリ・ハット報告は、単なる個人の注意不足を責める道具ではなく、現場からの“予防メッセージ”です。それを受け取って改善につなげるプロセスを整え、「気づき=評価される行動」という認識を浸透させることが、事故ゼロの文化づくりの礎になります。食品業の現場は、一見すると“慣れた作業”の積み重ねに見えますが、だからこそ小さなズレが連鎖しやすく、事故にも品質トラブルにも発展しやすいのです。ヒヤリ・ハットを通じて、「安全と品質は表裏一体」であるという現場感覚を、従業員全員が日々更新し続けられる仕組みが、真に事故を未然に防ぐ現場づくりのカギです。
以下に、「ヒヤリ・ハット活用チェックリスト(現場用)」を作成しました。現場点検・安全活動の促進・従業員との共有に活用いただける形式です。
▲ヒヤリ・ハット活用チェックリスト(現場用)
活用アドバイス
- 安全衛生委員会や定例ミーティングの中で定期チェックを推奨
- 「一番心に残ったヒヤリ」投稿ボードやMVP展示でモチベーション向上
- 「一番心に残ったヒヤリ」投稿ボードやMVP展示でモチベーション向上
是非ご活用ください。
4. IT活用で実現する“仕組みとしての安全文化”
食品製造現場において、ITツールは安全文化を根づかせる“後押し役”として、ますます重要性を増しています。ただし、ITは万能の解決策ではありません。現場の実態に即した設計と、使われ続ける仕組みづくり=運用設計こそが、真に効果を発揮させる鍵となります。
4-1. ITの力で“属人対応”から“再現性のある安全文化”へ
これまで、ヒヤリ・ハットの報告や点検作業、教育訓練といった安全活動の多くは、紙ベース・個人裁量に依存してきました。しかし、人手不足や外国人・パート社員の増加により、「誰がやっても安全」な仕組みづくりが求められるようになっています。ITは、属人的だった安全管理を“再現性のある仕組み”へと転換する力を持っています。
4-2. 現場で実践される3つのITツールとその効果
以下は、多くの食品製造現場で導入が進み、実際に効果が報告されている3つの代表的なITツールです。
▲3つの代表的なITツール
食品製造業での導入事例と工夫
- 中小企業でも導入可能
多くのクラウド型安全ツールは無料〜月額数千円で利用可能。専用アプリ不要で、個人スマホからのアクセスにも対応。 - 視覚的UI設計で教育効果アップ
文字だけでなく、写真・動画・音声を活用することで、外国人や非熟練者にも伝わる教育が可能に。 - 「記録のため」から「改善のため」へ
デジタルデータが蓄積されることで、ヒヤリ発生傾向の分析や、再発率の“見える化”が実現。 - 記録漏れゼロ運動
タブレット未入力項目がアラート表示される設計で、「抜け」がゼロに近づいた事例も。
4-3. ツール導入=目的ではない。「習慣化」と「現場主導の活用」がゴール
最も重要なのは、「ツールを入れること」そのものではなく、それを日々の現場で使い続け、改善に活かす習慣をどう設計するかです。
運用定着のポイントは、以下の通りです:
- 管理職が先に使う(トップの実践)
- “入力するだけで報告になる”など、手間を増やさない工夫
- 月1回のレビューとフィードバックで、活用成果を“見せる”
- 現場主導で改善提案が生まれる仕組みに(例:安全MVP制度)
4-4. “紙からの脱却”は、未来の安全文化への一歩
食品製造業の安全は、一人の努力では成り立ちません。誰でも・どこでも・同じ水準で安全を守れる仕組みをつくることが、持続的な安全文化の確立につながります。ITツールはその“基盤”です。属人性に頼らず、「人を守る仕組み」そのものをどう組み込むか——それが、安全文化の次なる進化です。
5. 成功する職場の共通点 ― 善意ではなく“仕掛け”で守る
どれだけ意識が高くても、人はうっかりする生き物です。疲労、習慣、焦り、思い込み——そうしたヒューマンエラーを前提に、「人の善意」ではなく“仕掛け”で守る文化をいかに作るか。それが、事故ゼロを目指す現場における“構造的な安全”の鍵になります。
5-1. 安全は、ルールではなく「行動として定着」してこそ
成功している食品工場の現場では、安全が“業務の一部”として染み込んでいます。
たとえば:
- 指差呼称・5Sを「始業前の5分ルーティン」として組み込む
→ 頭と体を“安全モード”に切り替える“儀式”として機能 - 多言語・イラスト・動画による作業ルールの視覚化
→ 派遣・外国人・初心者でも迷わず守れる環境づくり - 管理職が「危ないことはさせない」を“毎日口に出す”文化
→ 空気ではなく“言語化”で安全意識を伝承する
安全を「言われたからやる」ではなく、“やらないと気持ち悪い”習慣にまで昇華する仕掛けが、職場を支えているのです。
5-2. 食品工場ならではの「事故の芽」は、仕掛けで先手を打つ
食品製造業では、加熱・冷却・洗浄・回転体など、多種多様な危険因子が混在します。そのため、本質的安全措置+運用ルールの“合わせ技”で管理することが不可欠です。
以下は、現場で「守られている仕掛け」の一例です:
▲現場で「守られている仕掛け」の一例
構造で守るとは、“誰がやっても同じ結果になるようにすること”。属人的な注意喚起ではなく、環境と仕組みで“守らせる”文化がそこにはあります。
5-3. 「点検=チェック」ではない、「気づき=変化を拾う力」へ
よくある落とし穴が「点検=やったか/やってないか」のチェックリスト運用です。しかし、事故を防ぐには「何が変わったか」に気づく視点が不可欠です。
- 日々の点検に「昨日との違い」を1点記録する欄を設ける
- 「異常なし」で済ませず、「“正常”とは何か?」を現場で共有する
- 変化に気づいた社員を“気づき表彰”や朝礼コメントで称える文化
こうした積み重ねが、現場の“センサー感度”を底上げする土壌となります。
5-4. 善意ではなく「仕掛け」で守る、その理由
善意ややる気に頼らない、安全を“人ではなく構造で支える”ための工夫こそが、事故を未然に防ぎ、現場に安心と信頼を根づかせます。「誰かの注意力」ではなく、「誰でも守れる仕組み」があるか?それが、成功している現場に共通する本質です。
以下に、第5章「成功する職場の共通点 ― 善意ではなく“仕掛け”で守る」に対応した2種類のツールをご用意しました。ご活用ください。
▲現場改善チェックリスト
▲仕組み導入ステップ例(文化として定着させるために)
6. 「安全」を働き方改革の起点に ― “守るため”から“伸ばすため”の戦略へ
「働き方改革」と聞くと、多くの人がオフィスワーカー向けの在宅勤務や時短勤務、ペーパーレス化を思い浮かべるかもしれません。しかし、食品製造という現場のリアルを見つめたとき、その本質は「安全」にこそあります。
6-1. 安全が、働き方改革の“土台”である理由
食品工場では、加熱・冷却・高速回転体・刃物・蒸気・水・洗剤・狭所作業など、多岐にわたるリスクが交錯します。ここで「働きやすさ」を追求するには、まず第一に「安心して働ける状態」であることが不可欠です。安全性の高い職場こそが、持続可能な人材確保・定着・育成の“前提条件”なのです。
▲安全投資の“波及効果” ― 単なるコストではない
6-2. 「若手を巻き込む安全活動」が変える職場の空気
特筆すべきは、安全活動そのものが“人材育成の場”となることです。例えば、安全週間の企画やKY(危険予知)ミーティングのリード、安全ポスターの制作など、これまでベテラン中心だった“安全”に若手を巻き込むことで、
- 発言力・改善意識の向上
- 上下関係を越えた対話の場づくり
- 「守られる側」から「守る側」への意識変化
といった、安全を軸とした成長機会が創出されます。結果として、マネジメント人材の早期育成にもつながり、企業としての“底力”を強める原動力になります。
6-3. 安全は「守りのコスト」ではない ― 中小企業こそ攻めの戦略に
多くの中小食品工場では、「安全への投資は余裕のある大企業がするもの」と思われがちです。しかし、限られた人数で最大の品質・信頼を確保する必要がある中小企業にこそ、“安全”は投資効果の高い分野です。
- 離職による教育再コスト
- 事故対応による生産停止・賠償リスク
- 行政指導・信頼喪失のブランドリスク
これらを未然に防ぐ“安全戦略”は、将来の利益を守る経営判断そのものです。
6-4. 安全が、働き方を変える。
「安全=守るためのコスト」ではなく、「信頼・人材定着・品質を支える“成長戦略”」へ。食品製造の現場において、“安全”はもっとも基礎であり、もっとも先進的な働き方改革です。そしてそれは、「守る」から「伸ばす」への視点転換によって初めて、本当の価値を持ち始めます。企業の競争力は、こうした小さな仕組みから静かに、しかし確実に育っていきます。
終章:制度・週間を“活かす”ために必要な視点
2025年6月の熱中症対策義務化、そして7月の全国安全週間。いずれも“安全”を強化する制度・文化的な節目として位置づけられています。しかし、制度があっても現場が動かなければ実効性は得られません。また、安全週間が形式にとどまれば、定着するはずの文化は根づきません。本稿で示したように、現場で安全を機能させる鍵は「仕組み化」と「継続性」です。
- 一時的な施策ではなく、日常業務に組み込まれた“仕掛け”
- 負担で終わらせず、ITやルール整備で“再現可能”にする設計
- 訓練・教育・改善サイクルが、習慣として回り続ける状態
こうした考え方があって初めて、法令や週間といった「外側からの枠組み」は、現場の力として活用されます。義務と週間を“やらされるもの”から“使いこなすもの”へ。その発想の転換を、いま一度、自職場から始めてみませんか。
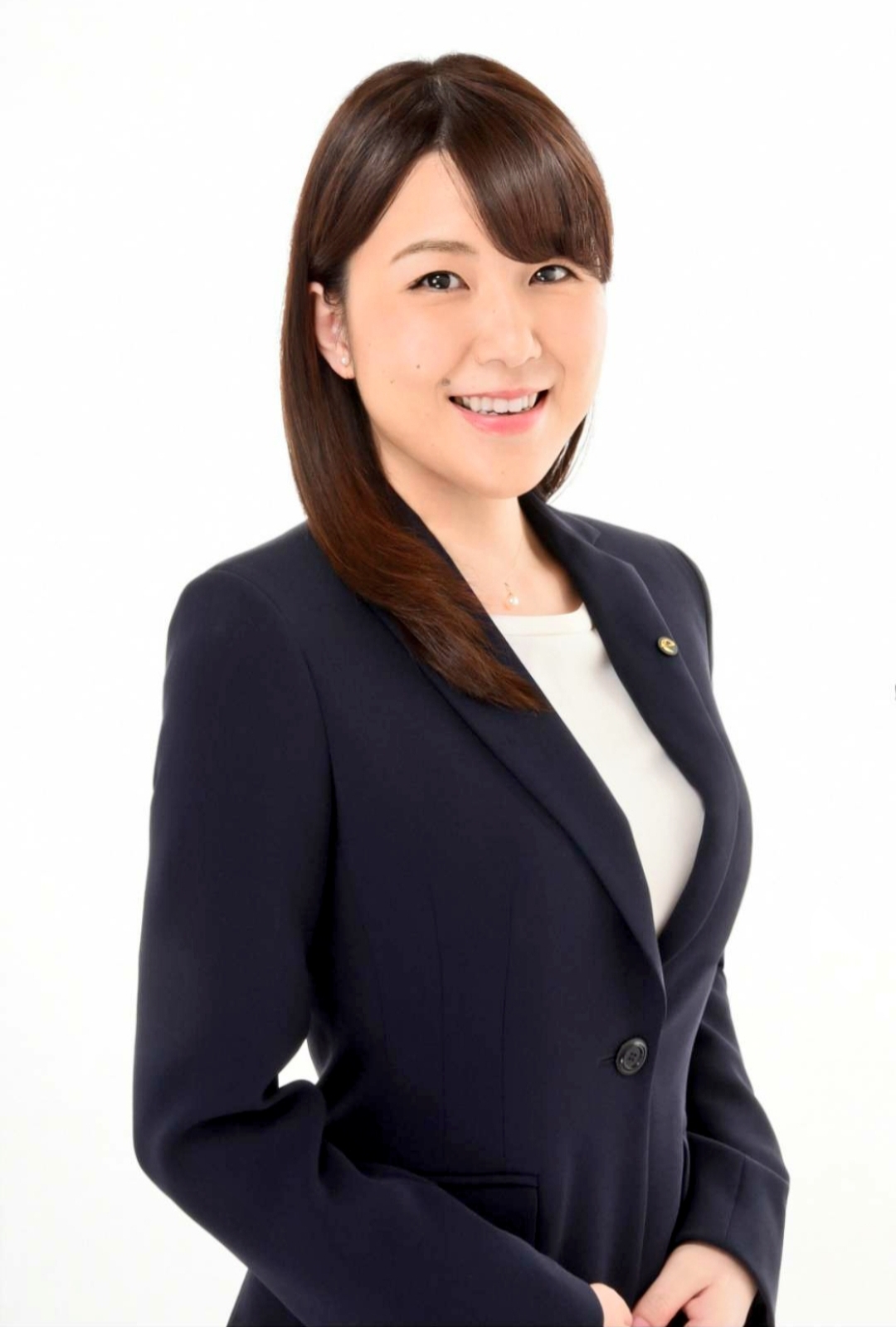
利益改善コンサルタント
資格・スキル活用コンサルタント
技術士合格講師
小松 加奈 氏
日系大手製造業に勤務しながら(2007年新卒入社、技術系総合職)、複業として個人事業も展開している。
工場現場担当者の経験もある、現役会社員の技術士。最前線で『リアルタイム』の『現場』『現物』『現実』『最新技術』と日々向き合っている。
勤務先では、開発部・工場(開発課・製造課・生産管理課)・商品部・生産本部生産管理部にて、工場現場から、本部での管理業務、生産原価管理システム構築、新設工場の生産管理業務構築まで務める。原価改善プロジェクト多数実施。改善・原価教育多数実施。
個人事業では「製造業特化型コンサルティング」「完全カスタマイズ型コンサルティング(全業種対象)」「資格・スキル活用コンサルティング」「技術士合格講座(一般部門全20部門対象)」を展開。
科学技術分野の文部科学大臣表彰(文部科学省主宰)の技術審査員も務め、400件以上の製造業改善事例を審査。
利益改善に関するコンサルティングや、合格に導く技術士受験指導にも定評がある。
【 資格 】
技術士(経営工学部門)、第一種衛生管理者、ハム・ソーセージ・ベーコン製造技能士、フォークリフト運転技能、フードコーディネーター 他
利益改善コンサルタント 技術士 小松加奈website
24時間を楽にする技術【技術士 経営工学部門 小松加奈】
技術士が経営工学技術をもとに、『24時間公私ともに楽にする技術』を『誰でも今すぐ使える』形でわかりやすく伝授❗❗
【2週間ごとに金曜日19時投稿】
【本コラムに関する免責事項】
当サイトへの情報・資料の掲載には注意を払っておりますが、
最新性、有用性等その他一切の事項についていかなる保証をするものではありません。
また、当サイトに掲載している情報には、第三者が提供している情報が含まれていますが、
これらは皆さまの便宜のために提供しているものであり、
当サイトに掲載した情報によって万一閲覧者が被ったいかなる損害についても、
当社および当社に情報を提供している第三者は一切の責任を負うものではありません。
また第三者が提供している情報が含まれている性質上、
掲載内容に関するお問い合わせに対応できない場合もございますので予めご了承ください。