1.はじめに
本連載コラムでは、食品製造業様に向けて、原価管理やKPIマネジメントなどの手法をプロジェクト事例も交えながら、経営管理の効果を高めるための情報として解説してまいりました。筆者は初回寄稿「食品製造業に求められる原価管理の取り組み」のなかで、食品製造業様における原価管理の重要性をご説明し、製品別ロット別の原価算定の詳細については、別の機械に稿を改めてと記載しておりました。その具体的な内容につきましては、前回投稿「食品OEMメーカーの原価管理改革への挑戦」に記載しておりますので、ご覧頂ければ幸いです。
原価管理の取り組みの重要性と役立ちについては、これまでの寄稿にてご理解頂けるものと考えておりますが、その実現のためには、製造に関する投入量や作業時間などの実績記録をデータ化することが必要になります。ロット管理やトレーサビリティの確保などが既に実現できている会社であれば可能ですが、これらが未完了の場合、どのように手を付けていけばよいのかイメージが持てないという感想を伺うことがあるのも事実です。
そこで、本稿では、主に原価管理の基礎となる実績把握の重要性と取り組み方、また、そのデータ化とシステムの関係について述べたいと思います。
2.食品製造業の現状と原価管理の重要性について
初回寄稿でも述べましたが、食品製造業では、新商品開発に力を入れつつも、製造面では熟練のパート従業員の技能に頼りながら操業を続けている会社が多いのではないかと思われます。結果、現状、下記の状況が多くの会社にあてはまるのではないでしょうか。
- 多品種少量生産の傾向が強い
- 工場内は、労働集約型のプロセスが多く残っている
- 食品安全性確保の観点より遵守すべき規則が多い
このような状況であれば、製品別原価(及び利益)算定の重要性は非常に高いと考えられます。多品種である結果、個別にみれば儲かっている商品と儲かっていない(中には赤字も)商品があると思われますが、分かっていれば改善の手が打てるものの、分からなければズルズルと困った状況を続けてしまいがちです。また、多品種少量生産である結果、段取りや洗浄の時間が増えている影響も把握したいところです。(図1参照)
3.腹落ちする製品別原価の把握のために
ここで重要視している製品別原価は、会計上で締めた費用を数量で配賦した計算結果というイメージではなく、以下の情報を反映した製品別の個性を反映した原価になります。
- レシピ
- 生産能力と稼働率
- 歩留率と廃棄実績
- 作業能率
①のレシピは、ある製品の生産のために投入される原材料や資材と、それぞれの投入量になります。製品別の材料費と売上高や付加価値の関係を把握するためには、これを事前に明確にしておくことが重要です。一般の製造業に例えるとBOM(部品構成表)にあたります。あわせて材料単価を登録しておけば、標準の材料費が明確になります。(図2参照)
このレシピの情報がしっかりと登録されていない、データ化されていないという会社は、早急に整備する必要がありますし、また、材料単価の変動に応じた見直しが出来ていないという会社は、運用方法を見直す必要があるでしょう。製品の開発段階で決定したレシピを登録し、以降、材料単価も含めてメンテナンスしていくことが重要です。
②③④のうち、生産能力については、工場(もしくは分けて見る場合は工程ごと)の能力を月産XX,XXX個といった要領であらかじめ指標として把握しておきます。これは、実際の生産量が能力に対してどれぐらいの稼働にあたるかを掴むためです。生産能力以外の稼働状況、歩留率、廃棄実績、作業能率は、日々の作業時間や出来高等の実績記録のデータから把握する指標になります。
稼働状況は、生産能力に対する実際の生産量の比率で把握することができます。
歩留率は、投入した原材料と出来高の比率になります。事前に上記のレシピを明確にしておけば、実際投入量とレシピ上の標準投入量を比較することが可能になり、歩留率の評価が可能になります。原材料費と売価のバランスが重要な食品製造業では、特に重要な視点であると考えられます。
廃棄実績は、製造工程における廃棄の記録です。歩留率の評価の際、差異原因の分析時に併せて検討する必要があると考えられます。食品製造業の場合、廃棄ロスの削減が利益の改善に直結しますので、これも重要な視点です。
作業能率は、人の作業時間あたりの出来高数量です。労働集約型の現場の場合は、実績記録を通じて見える化し、改善指標として意識付けしていくことが重要です。
4.腹落ちのために必要な実績記録の取り方
実際に、現場の実績を記録し、そこから上記の指標を把握していくためには、少なくとも日報などを記入して頂き、それを入力するなどしてデータ化する必要があります。実現すれば、そのデータを使った製品別原価(実際原価)の算定に繋がります。
例えば図3のような作業日報を記入し、その内容をデータ化して上記の指標を把握することが考えられます。必ずしも個人別に詳細に日報をつける必要はなく、ラインごとや工程ごとなど、管理上意味のある区分でリーダーもしくは管理者にあたる方が纏めて記入すれば十分です。大手食品製造業でなくても、各社、何らかの形式で作業日報は付けておられるのではないでしょうか。そのデータ化と活用まで考えた場合、下図を参考にして記入項目などを見直して頂ければと思います。
実際には、日々日報を記入してデータ化していくというのは、それなりの負荷がかかる作業になります。記入や入力の手間は工程区分や作業区分をどれだけ詳細に区分するかにもよりますが、仕組みとして継続することを考えると、どこかの時点で、紙ではなくタブレット端末を導入して入力作業を無くすことも検討すべきです。
5.仕組みづくりの考え方
実績記録の分析と活用のためには、上記各指標の把握に加えて、それらを使って製品別原価(実際原価)の算定までつなげる必要があります。
計算方法は、概略、材料費は製品別の投入実績(単価×数量)を反映させて、加工費は労務費・経費を時間あたりで把握し、製品別の実際作業時間(段取時間+作業時間)で配賦します。
これによって、材料費については、レシピに基づく投入実績によって製品別材料費が計算され、それが標準と比較可能な仕組みになります。加工費については、稼働率があがれば製品に配賦される時間単価(チャージレート)が下がることで加工費が下がる仕組み、能率があがれば製品1個当たりの作業時間が減少することで加工費が下がる仕組み、同様に段取り時間が短縮されれば能率があがって加工費が下がる仕組み、となることで、実績記録と製品別原価が関係づけられ、現場改善が動機づけられるのが狙いです。
これを実現させるシステムイメージは図4のとおりです。試行錯誤しながら仕組みを作っていく場合には左のような進め方になりますが、理想形は右図のとおりです。原価管理の基礎になる生産管理システムを導入される際に、上記の目線で原価管理の要件もしっかりと構想に加えて頂いて、導入パッケージの選択をすることが重要と考えられます。
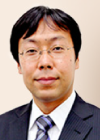
川上 徹 氏
【専門領域】
●原価管理/採算管理制度の企画・設計と導入・定着化支援
●管理会計制度等の経営管理制度の企画・設計と導入・定着化支援
●業績改善・事業改善に向けた計画策定と実行支援
【経歴】
新日本監査法人を経て、(株)アットストリームに参画。
現在、アットストリームパートナーズ合同会社のパートナー。公認会計士。
【書籍】
・図説 生産現場で使える原価管理の仕組み(共著)(日本能率協会コンサルティング)
・現場管理者のための原価管理の基本(共著)(日本能率協会マネジメントセンター)
・「製造業」に対する目利き能力を高める(共著)(金融財政事情研究会)
【本コラムに関する免責事項】
当サイトへの情報・資料の掲載には注意を払っておりますが、
最新性、有用性等その他一切の事項についていかなる保証をするものではありません。
また、当サイトに掲載している情報には、第三者が提供している情報が含まれていますが、
これらは皆さまの便宜のために提供しているものであり、
当サイトに掲載した情報によって万一閲覧者が被ったいかなる損害についても、
当社および当社に情報を提供している第三者は一切の責任を負うものではありません。
また第三者が提供している情報が含まれている性質上、
掲載内容に関するお問い合わせに対応できない場合もございますので予めご了承ください。