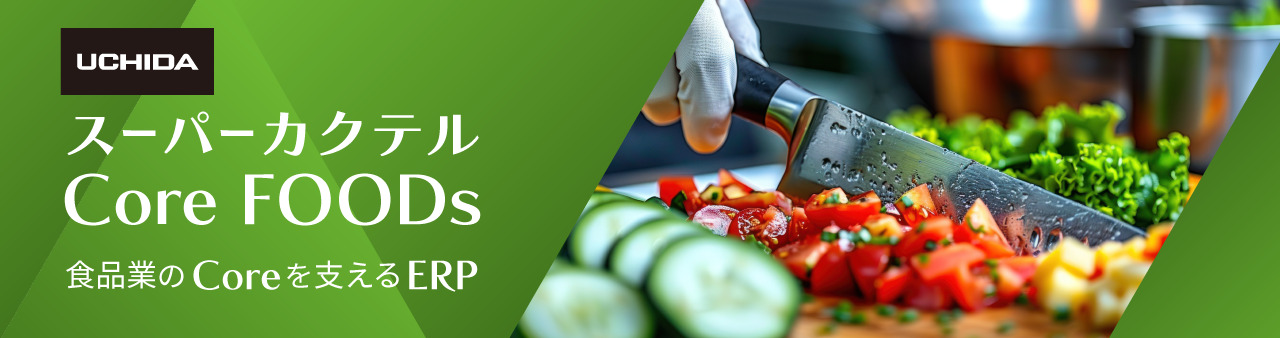
スマートファクトリーの推進
食を取りまく外部環境は刻々と変化し、企業は柔軟な対応が必要とされます。従来の課題である人手不足や施設インフラの老朽化、製造コストの削減のほか、環境変化に伴う付加価値の創造や品質向上等、製造現場の課題は尽きません。これらの課題を解決するために、製造現場にIoTやAIを導入する「スマート工場(ファクトリー)」に取り組む企業が増加しています。
スマートファクトリーとは
製造作業を人の手からロボットへ移行し、IT技術を活用することでヒトの負担を軽減する取り組みです。経済産業省「ものづくり白書」2019年度版によると、製造プロセスのデータ化や自動化の実施状況は「可能であれば実施したい」企業の割合は増加しているものの、実際に実施している、もしくは実施する計画があるという企業の割合は増えていません。IoT導入の必要性を感じているものの、実行には至っていないということです。
食品製造業のスマート化ロードマップ
製造現場をスマート化するために、まずはどの課題を解決したいか、課題に優先順位をつけることが重要です。あれもこれもと、解決したい課題を絞り込まずにIoTをとにかく導入してしまうと、どれも中途半端に終わってしまう可能性があります。スマート化によって目指す目的と、そのために必要となる工程について、下記のような例が挙げられます。
品質の向上
不良率の低減
作業手順や結果をセンシングしミスを削減します。過去に発生した異常について分析し、どの工程で発生するのか特定することでレシピ変更や人員配置変更を行います。
品質の安定化・バラつきの低減
製造設備にセンサーを搭載しデータ収集してモニタリングします。収集したデータを用いて、バラつきの要因特定や加工性能の最大化を図ります。
設計品質の向上
製品にセンサーや通信機器を搭載し、使用状況等のデータを収集します。品質向上や顧客満足度向上のため、レシピの仕様や生産方法の改善を図ります。
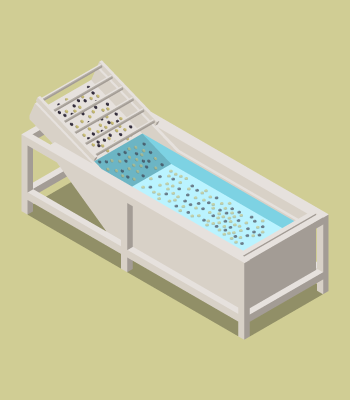
コストの削減
材料の使用料の削減
過去のレシピを解析し、使用する材料の削減・変更を行い材料コストの最小化を図ります。
生産のためのリソース削減
製造実行システムデータを利用し、人的コストや製造エネルギーの最小化を図ります。
在庫の削減
受注~出荷の計画や実績を分析し、需要変動の要因特定および予測を行います。予測した需給データに基づき、原材料調達や生産計画、出荷計画の最適化を図ります。
設備の管理・状況把握の省力化
製造設備にセンサーを搭載し、稼働状況をいつでも把握できるようにします。トラブル発生時に素早く対応し、監視・点検等の管理業務にかかるコストを削減します。
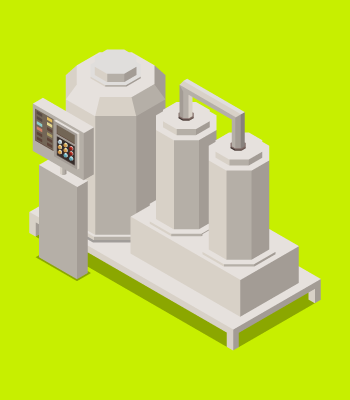
生産性の向上
設備・ヒトの稼働率向上
製造実行システムで現場全体の稼働状況や従業員の作業進捗を把握することで、各作業完了時間を予測します。設備・従業員の非稼働時間の発生要因を分析し、稼働率向上を実現します。
ヒトの作業の効率化、作業削減・負担軽減
HMIやRFID等を活用することで、生産情報や設備稼働状況などデータ入力・確認することが可能となります。
設備故障に伴う稼働停止の削減
センサーや無線通信機を製造設備に搭載することで、故障に繋がる予兆や条件に合わせて故障発生時期を予測することが可能です。
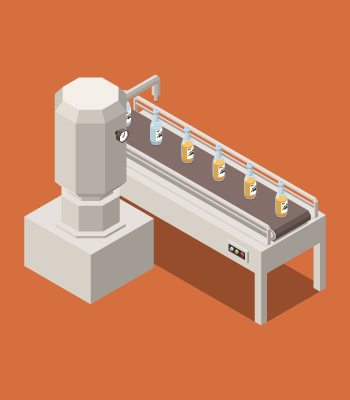
解決したい課題を絞り込んだ後は、「データ収集・蓄積」「データによる分析・予測」「データによる制御・最適化」と3つのステップでスマート化のロードマップを作成します。ロードマップを作成することで、各フェーズにツールは必要か、運用の改善で賄えるかを判断し、余分な設備投資を防止することが可能です。
食品品質向上を支援するソリューション
製造現場のスマート化は、生産性の向上や人手不足対策、製造品質の向上など多くのメリットがあります。食品衛生法が改正され、HACCP制度化が全面的に開始される等、食品の製造および加工・販売における安全性の確保や品質管理向上は現在よりもさらに重要視されます。自社で取り扱う製品の品質情報の管理について、今一度見直してみましょう。
本記事で紹介する食品品質情報管理システム「食Quality」は、製造に使用した原料の版数管理や配合、製品の原価・栄養計算等、品質情報をデータベースで一元管理します。複雑な製品・原料の品質情報を一元管理できるので、業務を効率化することが可能です。また、問合せ発生時には、得意先や一般消費者へ迅速に回答が可能となり顧客満足度の向上にも繋がります。